Off-site chronicles with Craig Mitchell, Modular and Offsite Construction Consultant, BlackBox Offsite Solutions
Author: OCRC
Posted on Apr 27, 2023
Category: Off-site chronicles
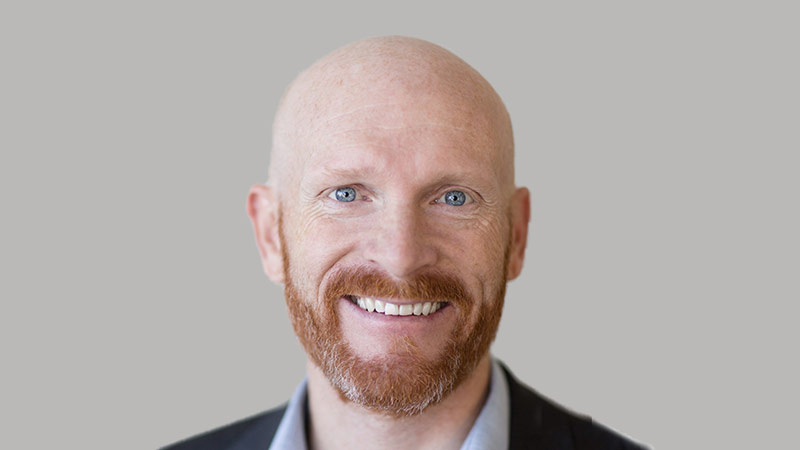
Craig Mitchell is an experienced modular building professional and a graduate of both the University of British Columbia (UBC) and of British Columbia Institute of Technology (BCIT). Craig has been a part of the construction industry for almost 30 years, with 24 years of them being devoted to the modular building sector.
For the past ten years, he has been a key member of several senior management teams and most recently was one of the leaders who led the strategic transformation of an existing modular business into a Permanent Modular construction leader. In recent years, he has ventured into his own off-site construction consultancy, BlackBox Offsite Solutions and also joined 720 Solutions to focus on building modular affordable housing projects across Canada.
In this conversation with Craig, we discuss with him his journey and his take on the future of off-site construction.
What inspired you to start BlackBox Offsite Solutions and join 720 Solutions?
I like building projects. Period. Throughout my career, the one area of modular construction projects that have been severely lacking is the coordination between consultant teams, the modular factory, the site team and the owner. I’ve been part of project teams during my career where projects have gone really well, and others that have gone sideways. The one commonality between all of them is the level of communication and integration among the people on the team. Off-site construction requires a tremendous amount of communication and integration. I bring my leadership and knowledge of what works in modular construction to my clients.
Can you give us a bit of background on the services BlackBox Offsite and 720 Solutions offer? What unique value proposition do you bring to the off-site construction industry?
We offer a collaborative approach to construction. Using a football analogy, we act as the Quarterback for any of our modular projects. Even though modular construction has been around for over 50 years in Canada, it’s only in the last five to seven years that we have seen growth in a new wave of drivers for permanent modular construction (PMC) projects. Because these types of PMC projects are more complex than what had previously been built in Canada (think workforce accommodations), there is a lack of knowledge about how to integrate modular construction into mainstream construction. By taking a lead role and bringing teams to the table early, these projects are much more successful than if they are left to follow a traditional construction process.
Modular Rapid Response Affordable Housing Project.PNG
What are some of the biggest challenges in the modular building industry? How are BlackBox Offsite and 720 Solutions helping to overcome those challenges?
Some of the biggest hurdles and challenges of the modular building industry in Canada is the lack of knowledge among owners and consultants on how to execute a modular project effectively. I would also add there is a lack of capacity among commercial modular companies. I have always been an advocate for the modular industry in trying to build capacity and educate those interested in exploring off-site construction. “A rising tide floats all boats” is a mantra I live by. By creating a healthy thriving industry that is growing will allow more projects to get built effectively and will create the ability to solve some of our housing issues we have in this country.
In your experience, how have you seen off-site construction evolve over the years, and what significant innovations have contributed to its growth?
Off-site construction has grown from a very fringe construction methodology to one that is now being discussed at early project inception. It was often the assumption that a project would be built traditionally from the ground up with the options of wood, steel, or concrete. The question of “HOW” the project is being built is now part of that early project discussion and owners and construction teams are seeing value in moving part of the construction process off-site. There will always be a site element to construction, but if there is the opportunity to have greater control over the construction process and de-risk the project by moving part of it off-site, owners are beginning to see great value in that.
On the innovation front, we are starting to see more capital investment coming into the prefabrication market in Canada, especially in mass timber. We are also seeing the utilization of robotics and automated wall lines in panel factories in Canada (even though the Europeans have been using this technology for over 15 years now). Modular hasn’t seen the same amount of capital investment as the other two mentioned, but there are a number of new startups entering the marketplace. Modular has seen a much more cyclical market over its history here in Canada which has resulted in a lack of sustained capital investment. I hope that we’ll see a similar growth model in this sector as what is happening in the US right now.
First Multi Family Modular Passive House in Canada
What are some of the common misconceptions about off-site construction that you have encountered?
First and foremost, people think off-site construction costs less than traditional construction. Generally speaking, it isn’t the case. There is an argument that it is cost neutral, but the real benefit is the speed, quality, and cost certainty that comes with a properly executed off-site project. The other misconception is that it is easy to convert a traditional construction project to an off-site project midway through the design stage. Off-site construction only works when the decision by the owner to go off-site is done early on at the schematic design stage. Any later will result in re-designing and re-engineering the project to adapt to off-site construction.
What role does technology play in off-site construction in general, and more specifically in your organization? How do you see it impacting the industry as we move forward?
We are starting to see tremendous benefits in digital modelling of the building and sharing the model among all parties in the project. From consultants right down to the manufacturer, having a consistent model that is reviewed early on prior to actual construction removes many of the headaches faced by 2D drawings. We are currently using Autodesk Revit for most of our projects and the factories we work with are working in a more detailed level of design than what would be the norm in traditional construction. I see the industry continuing to move forward with better and better digital tools. I can’t wait to see where AI takes us!
Are there any future plans or developments in the works for BlackBox Offsite or 720 Solutions that you can share with us?
We want to make a dent in the affordable housing crisis here in Canada. This means establishing a better framework and a model from which to grow the adoption of modular construction for the government and agencies in this sector. Stay tuned for more in this area.
First 6 Storey Modular Micro Apartments in Seattle
What advice would you give to someone considering a career in the modular building industry?
Because the pool of professionals in the modular industry is quite small, I see some tremendous opportunity for those entering this industry. I see great opportunities for someone who is savvy in technology, a good communicator, has some traditional construction experience or is interested in construction in general, and someone who has an appetite for knowledge and innovation.
What do you think is the next big thing in modular construction that will disrupt the industry?
There are a few areas I’m keeping my eye on right now that are beginning to make inroads into this industry in Canada.
1. Robotics in construction: this is happening in the US right now in several factories there. We’re also seeing it in panel construction here with some factories in Canada. This will be a game changer that will increase quality and drive down cost.
2. Use of mass timber in volumetric modular construction: Ellis Don is currently working on prototypes in this area, and there are a number of manufacturers in Europe who are currently in this space.
3. Global supply chain: We are going to start seeing more offshore companies starting to enter our market. We already have and this will begin to grow.
Please tell us about your professional journey. Did you always know you will end up in modular buildings? How different is it from the initial path you chose?
Believe it or not, I wanted to become an urban planner. I graduated with a degree in Urban Geography and was about to embark on getting my Masters in Urban Planning before I came to my senses (apologies to all those urban planners out there!). I really liked the construction and the technical aspects of the industry.
I actually worked in the construction supply industry while going to school which led me to eventually get a diploma in Technical Sales from BCIT’s School of Business. I got hired as a technical sales rep with a growing and innovative modular manufacturing company right out of school 27 years ago and the rest is history. I’ve loved the problem-solving aspect of the industry and the uniqueness of the projects and the different drivers of the owners who choose modular as their method of construction.