What is off-site construction and how does it work?
Author: OCRC
Posted on Jul 4, 2024
Category: Off-site Construction
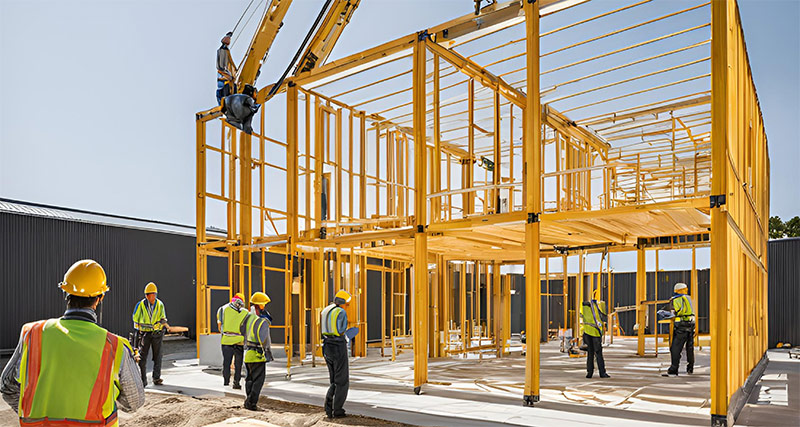
If you're in the construction industry or considering a new building project, you've probably heard the term "off-site construction" tossed around. But what exactly is it, and how does it work?
What is off-site construction?
Off-site construction, also known as modular or prefabricated construction, is a method where building components are manufactured and assembled away from the actual construction site. Think of it like assembling Lego blocks in a factory rather than on your living room floor. These components, often referred to as modules, are then transported to the construction site where they're pieced together to form a complete structure.
There are also different levels of pre-fabrication. “Off-site construction” captures anything from complete volumetric modules (like a modular home, or a hotel room unit), to panelized construction (i.e. Wall panels to assemble an apartment building), to pre-cast concrete. Regardless, the components are constructed in a facility off-site, then transported to the project site for final assembly.
How does it work?
The process of off-site construction can be boiled down to a few key steps:
1. Design and planning: Like any construction project, the process begins with detailed planning and design. However, the design phase for off-site construction often heavily relies on digital tools and technologies like Building Information Modeling (BIM) to ensure every component fits perfectly when assembled on-site. Additionally, a lot more upfront planning is required to deliver an off-site project to ensure that everything is built ahead of time off-site and can be delivered to the project site when needed.
2. Factory fabrication: Once the design is finalized, manufacturing can begin in the factory. Here, any prefabricated components are manufactured in a controlled environment. This factory setting allows for precise construction and stringent quality control, which can be harder to achieve on a traditional construction site. The added benefit is the fabrication of components can concur simultaneously with the groundwork happening at the project site, which can significantly reduce the project schedule.
3. Transportation: After fabrication, the manufactured components are transported to the construction site. This step requires detailed planning to ensure that the components arrive on time.
4. On-site assembly: Once the modules reach the site, they are assembled like giant building blocks. This phase is usually faster than traditional construction since the modules are pre-made. Think of it as piecing together a giant puzzle, where each piece has a specific place and function. Quality of components and ensuring the installation meets design tolerances is crucial at this stage.
5. Finishing touches: After assembly, the final touches are added, such as interior finishes, landscaping, and any site-specific adaptations. And voila! The building is complete, often in a fraction of the time it would take using traditional methods.
Why choose off-site construction?
There are several compelling reasons why off-site construction is gaining popularity:
- Speed: Because much of the work is done in a factory while site preparations are simultaneously underway, off-site construction can significantly reduce the overall project timeline.
- Quality control: Factory settings allow for better control over construction quality. Each module is built to precise specifications, which can result in a higher-quality finished product.
- Cost efficiency: Reduced construction time and improved quality control can lead to cost savings. Additionally, the factory environment minimizes waste and optimizes the use of materials.
- Safety: Working in a controlled factory environment reduces the risks associated with on-site construction, such as adverse weather conditions and site-specific hazards. Check out our research on Quantifying Safety in Off-site Construction
- Environmental impact: Off-site construction often results in less waste and can incorporate sustainable practices more easily, contributing to a greener building process.
Final thoughts
Off-site construction is revolutionizing the way we think about building. It's faster, more efficient, and often more sustainable than traditional methods. By leveraging modern technology and innovative practices, off-site construction is paving the way for the future of the industry.
Whether you're a construction professional, a developer, or someone interested in new building methods, off-site construction is worth exploring. It might just be the perfect solution for your next project!
Take a look at our project profiles to see real-world examples of off-site construction in action with our industry partners.
Interested in exploring the potential of off-site construction methods for your next project? Reach out to us at offsiteconstruction@unb.ca to see how we can help.