What are the different types of off-site construction?
Author: OCRC
Posted on Jul 31, 2024
Category: Off-site Construction
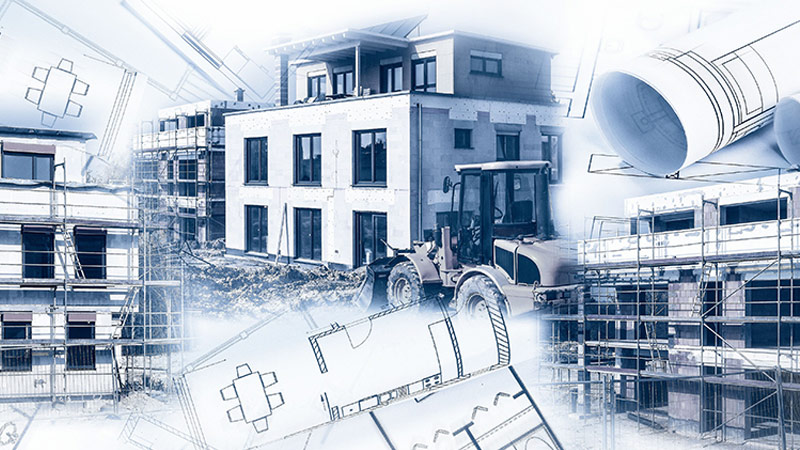
Off-site construction, often synonymous with terms like modular or prefabricated construction, involves manufacturing and assembling building components away from the actual construction site. This method offers numerous advantages, including reduced build times, enhanced quality control and cost savings. But did you know that off-site construction isn't a one-size-fits-all solution? In fact, there are four distinct types of off-site construction, each with its own unique benefits and applications.
In this blog, we'll delve into the four main types of off-site construction: Volumetric modular construction, panelized construction, hybrid modular construction and component (sub-assembly) construction. By understanding these different approaches, you'll be better equipped to select the most suitable method for your next project and leverage the full potential of off-site construction.
1. Volumetric modular construction
Volumetric modular construction involves the manufacturing of three-dimensional units, or modules, in a controlled factory environment. These modules can be fully or partially fitted out before being transported to the construction site. Most used for residential buildings, hotels, schools and healthcare facilities, this method of off-site construction observes benefits such as:
- Speeds up construction time as modules can be produced concurrently with site work
- Enhances quality control through factory conditions
- Reduces on-site labor and associated costs
A great example of this from right here in New Brunswick, is the Amsterdam Inn & Suites by Alantra Leasing.
2. Panelized construction
Panelized construction involves the production of flat panels, such as walls, floors and roof sections, which are then assembled on-site. Panels can be made from a variety of materials including wood, steel and concrete.
This application is suitable for residential homes, apartment buildings, commercial buildings and educational facilities.
Benefits of this method of off-site construction include:
- Increased flexibility in design and customization
- Reduces construction time compared to traditional methods
- Enhances precision and quality through factory manufacturing
3. Hybrid modular construction
Hybrid modular construction combines volumetric modules with panelized components. This approach allows for greater design flexibility and can optimize the use of both methods depending on the specific requirements of the project.
This method is ideal for complex projects like hospitals, multi-family housing, and large-scale commercial buildings and offers benefits such as:
- Maximizes the advantages of both volumetric and panelized construction
- Allows for more complex and customizable designs
- Can optimize construction efficiency and resource utilization
4. Component (sub-assembly) construction
In component construction, individual building components, such as stairs, bathroom pods, or mechanical and electrical assemblies, are manufactured off-site and then integrated into the main structure on-site.
You’ll find this commonly used in residential, commercial and industrial buildings. The benefits of using such methods include:
- Enhances quality control and consistency of specific building components
- Reduces on-site labor and installation time
- Improves safety by reducing the amount of high-risk work performed on-site
Summary
Off-site construction, through its various forms, offers a range of benefits including reduced construction time, improved quality control and cost savings. Each type of off-site construction method provides unique advantages and can be selected based on the specific needs and constraints of a project. By understanding and leveraging these different approaches, construction professionals can optimize their projects for efficiency, quality and sustainability.