Meet the chair: Dr. Hamed Asgari, Lockheed Martin Research Chair in Additive Manufacturing
Author: UNB Research
Posted on Jul 14, 2023
Category: Partnerships , Innovation & Commercialization , Research
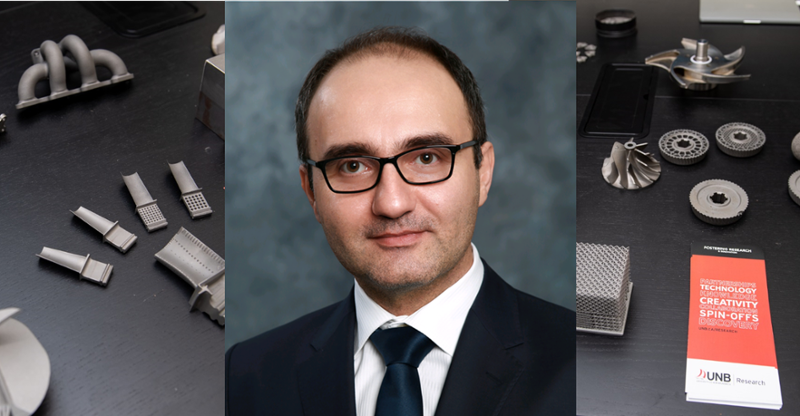
Dr. Hamed Asgari is an assistant professor of mechanical engineering and Lockheed Martin Research Chair in Additive Manufacturing at the University of New Brunswick (UNB). With his appointment, the university’s sector-leading expertise in marine additive manufacturing will get a new boost in capacity as Asgari takes metal-part fabrication from 3D printing to 4D.
4D printing involves creating parts using smart materials that adapt to the world around them – potentially enabling solar cells that, like flowers, turn themselves toward the sun, or ships that may subtly change their hull shape as water conditions change.
We spoke with Asgari to learn more about what this technology means for UNB, for manufacturing, and for the world.
Can you tell us a bit about yourself?
After receiving my PhD from the University of Saskatchewan in Saskatoon, I then joined the Marine Additive Manufacturing Center of Excellence (UNB) as a postdoctoral fellow and the Multi-Scale Additive Manufacturing Laboratory (University of Waterloo) as a research associate.
My main areas of research are metal additive manufacturing, alloy design, process optimization and materials characterization. In my research, I have closely collaborated with key aerospace, marine and energy companies such as Safran Landing Systems, J.D. Irving, Siemens, AP&C and Burloak Technologies on significant additive manufacturing projects. I am currently exploring the characteristics of 3D printed titanium and copper alloys at high impact velocities.
What will you be working on in your role as chair?
I will be focusing on additive manufacturing of metals, alloys and metal matrix composites. In additive manufacturing, we create objects by building them up from powder particles, rather than taking a block of material and removing parts of it (what we call ‘subtractive manufacturing,’ and includes techniques like CNC milling and gear cutting). Specifically, I am going to be looking at how we can use “smart” materials to enable new possibilities – something we call “4D printing.”
What exactly is 4D printing?
4D printing in an evolution of 3D printing. While 3D printing has many benefits, of course, the focus is on rigid or static parts. That is, a part is printed and is intended to remain exactly as it was made for as long as possible. With 4D printing, we want the parts we create to be dynamic or animated, not static.
To achieve these goals, we need to look at smart materials; the ones I am particularly interested in are called Shape Memory Alloys (SMA). These materials can be ‘programmed’ by controlling how and where they are used when we’re printing a part. When we say ‘programmed,’ however, we mean that we can cause the part to respond predictably to certain environmental features without relying on machine or human control.
So, for example, using an SMA that responds to heat – say, one composed of titanium, nickel and copper – a part might change its shape as the water temperature increases. We could also imagine a solar cell that is able to turn itself toward the sun, without a computer or a motor, based on how it responds to the sun’s heat in particular areas.
It sounds like these alloys have a lot of potential.
They certainly do. Among other areas, they open the door to new approaches to cleaner energy output and reduced greenhouse gas emissions through more efficient wind and solar energy generation and even by removing the dependency on hydrofluorocarbons (with high global warming potential) in current vapor-compression refrigeration systems.
In an emerging technique, called solid-state elastocaloric cooling, exerting and relieving stress on smart alloys can produce heating and cooling in systems through structural changes in these alloys. These are just some of the incredible characteristics of SMAs. Others include self-operating, folding, fitting, sensing and healing, which could enable 4D printing to offer cost-effective, light, and complicated smart components for various strategic sectors.
If we then combine these SMAs with another “intelligent” technology, namely artificial intelligence (AI), we can open doors to even more complex structures. We may create ship hulls that adapt to optimize their performance in response to water conditions, or manufacture morphing wings for drones and airplanes to increase their efficiency under different flight conditions.
By using AI technology, we should be able to iterate through different formulations of materials and different structures more quickly. That should let us get better results and smarter alloys, and because we will need to conduct fewer physical experiments, we should be able to get those results faster and more efficiently.
What do you think the impact of advanced 3D and 4D printing will be?
I believe that this is going to be a revolutionary technique that is used in every sector.
I don’t think it will replace existing technologies soon, but it will complement them and enable new approaches in many industries.
To be a part of this transformation, however, we will need to keep pace with new ideas and developments and invest in research and innovation. Even now, we’re behind Europe and the United States. Canadian firms are a bit more conservative in their approach to adopt AM technology.
We will need to invest in teaching and training, both to support the next generation of experts and to educate in-field professionals on the potential afforded by these tools.
I think we are ideally poised to do that. At UNB, we have all the ingredients: We have access to the top-tier equipment and infrastructure we need; we have the expertise and the creativity; we have students with an appetite to learn and grow; and we have relationships with industry partners that are open and excited about the possibilities. However, to capitalize on this opportunity, we will need to rely on support from our funding agencies and industry partners to develop this emerging technology.
More information
Dr. Hamed Asgari| Department of Mechanical Engineering | Faculty of Engineering
Research at UNB | Graduate Studies at UNB | Postdoctoral fellowships